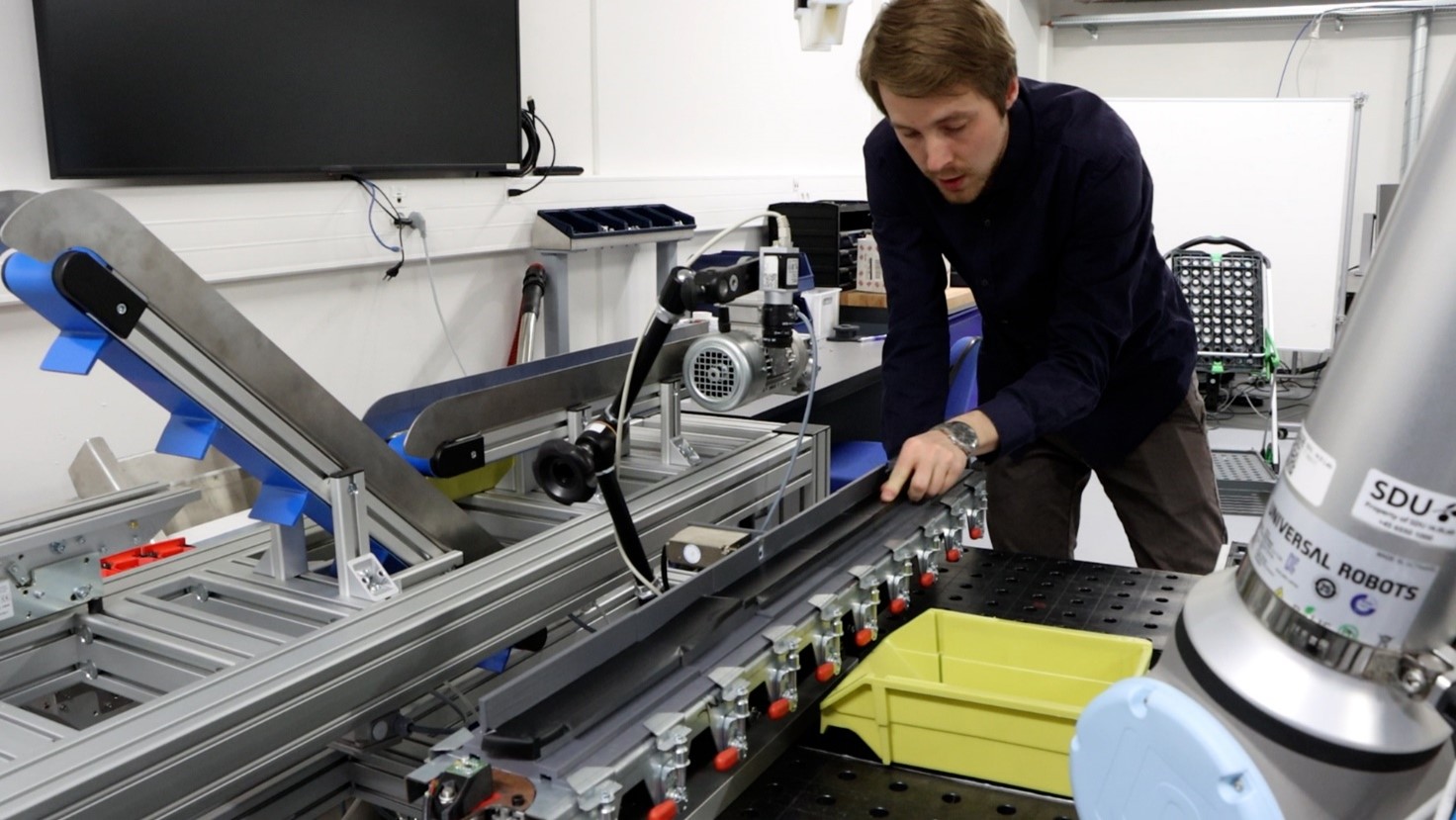
New Technology Aims to Make Production Cheaper and Smarter
At the Faculty of Engineering at the University of Southern Denmark (SDU), there is a wide-ranging collaboration underway that, with the assistance of modern technologies, aims to kickstart a minor revolution within the manufacturing industry.
For most people, the words "smarter component feeding technology" may not elicit a strong reaction, but for many companies across the country, they could mean significant cost savings and less hassle.
That's what Simon Faarvang Mathiesen, an associate professor at the University of Southern Denmark (SDU), is working on.
He is in the final stages of a nearly 10-year project as part of the production cluster MADE in collaboration with SDU, Danfoss, Lego Group, and Technicon, which has the potential to kickstart a minor revolution in the world of manufacturing.
Component feeding is the process in automated production where components are transported to a handling system, such as a robotic arm. It may sound simple, but for an automatic handling system to work, the components, or items, need to be oriented correctly and be in the right position.
Developing such a component feeding system can be both complicated and expensive, but Simon's technology can significantly simplify the process. Here, he explains how.
What is unique about your system?
Traditional component feeding is a physical challenge. One must ensure that items always orient correctly and are in the same position for blind picking. Our system accomplishes this, but we've introduced a way to set up a classic component feeding task much more easily by using smart technologies like simulation. Simulation is used to design the systems without having to build them first.
In addition to simulation, you also use artificial intelligence and 3D printing. Has it been challenging to make these technologies work together?
Yes, the challenge is that when we want to introduce a new item, a solution needs to be designed to ensure that the item orients correctly. What we've done in this system is to eliminate some of the complexity by using AI.
We have a camera-based solution that monitors whether items are oriented correctly. If they're not, a small mechanical stamp kicks them into the correct orientation. The more modern AI aspect is that we can train a neural network to recognize how items are oriented without having to program how it should recognize it. It learns that this is how it looks when it's oriented in this way, and this is how it looks when it's oriented differently. This way, we can automatically train the algorithm to monitor how items pass by.
Additionally, we simulate how items move in vibratory feeders. This ensures items are oriented correctly, so there's no need for a stamp to sort specific items. Here, we also use machine learning to optimize for the best possible performance.
So, the system where items go through and are sorted is developed by AI and then 3D printed?
Exactly. Instead of manually designing based on your best experience, testing and iterating until it works, we can simulate our way to a solution that achieves the correct orientation.
According to an article from MADE, it typically takes 200 engineering hours to develop a component feeding system. How long would it take for this system?
There will always be special cases where it takes longer than others, but we aim for an average implementation time where it takes a couple of days to find a solution, and then it needs to be 3D printed. It's simply a matter of setting it up for printing. It can take a few hours but depends largely on the 3D printer.
What's next for your project?
The project is actually nearing its conclusion. We've developed the core technologies needed, and now we're investigating how far we can go. In other words, where does it fail? Where does it succeed? Where does it make sense to apply this?
We're also in the process of building the hardware that supports our design process. We're not done with that yet. We're very keen on achieving what's called flexible automation. Here, you can use the same equipment for component feeding on various items to a significant extent.
There are many small and large Danish companies where it's not cost-effective to automate their production because the machines will eventually stand idle. We want to make it so that by changing small parts, you can use the same equipment for multiple tasks. It can run for four hours one day with one task, four hours the next day with something else. And you can move it around in the production because component feeding occurs in many places.
If you had to describe how significant this development is, what would you say?
The research results are promising, and if successful, which it seems likely to be, it could potentially be a brand new enabler for automating low- and medium-volume products. It could be quite substantial, but it depends on how it's received.