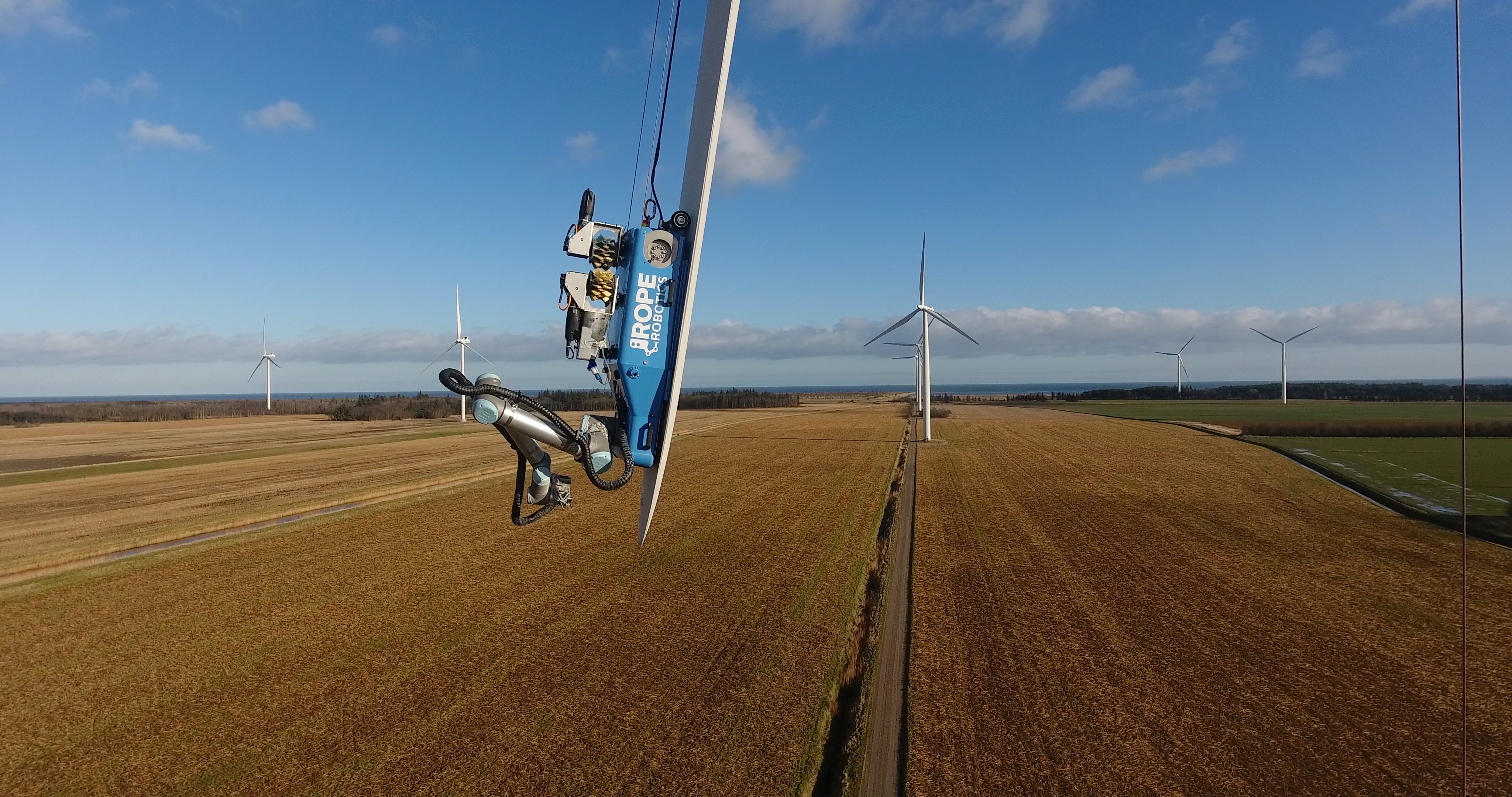
Robots make wind turbine maintenance faster, cheaper and more secure
A new project led by researchers at the University of Southern Denmark aims to develop a robot that enables technicians to maintain wind turbines without having to climb up into them and rappel down along the wings. Due to the enormous planned expansion of offshore wind, new solutions on the area are necessary.
During the next years and decades, a lot of wind turbines will be installed. As in: a lot.
For example, Danish production of electricity from offshore wind turbines is to be increased fivefold by 2030. In the entire North Sea region, politicians from Denmark, Germany, the Netherlands, and Belgium have set a goal to increase offshore wind capacity tenfold by 2050, and to install no fewer than 10,000 of the largest turbines. In the EU, wind capacity is expected to double by 2030. And then we haven't even mentioned countries like China, the US, and India, who are also investing heavily in wind energy.
However, something that is rarely heard about is that wind turbines need to be maintained.
For example, the leading edge of the blades must be regularly treated with a special type of coating to prevent erosion and unevenness. As it is now, this requires manual labor, and it is both cumbersome, expensive, and not entirely without safety risks. With the enormous planned expansion of wind energy, this is not a sustainable solution.
Advantageous robots
This is the problem that the research project SENSIBLE aims to solve.
The project is being carried out by researchers from the University of Southern Denmark and Aarhus University, as well as the companies Rope Robotics and Xplor XR. Together, they will develop a so-called teleoperative robot that can perform service tasks on wind turbines and be operated by technicians in a control room far away from the actual turbine.
Such a robot will have a wide range of advantages, explains Cheng Fang, who is an associate professor of robotics technology at the University of Southern Denmark and the project leader:
- First and foremost, technicians will have a better working environment. With the robot, maintenance work will also become more efficient, allowing more turbines to be serviced in a shorter amount of time, which also means that the turbines need to be shut down for shorter periods, Cheng Fang explains.
- The lifespan of the turbines will be extended when they are regularly maintained, and productivity will increase. And service tasks can be performed more days per year, including days when it is currently too windy.
More versatile and precise
The plan is to further develop a robot that already exists on the market and is patented by Rope Robotics. Currently, the robot works by being hoisted up along the wind turbine blades on a set of ropes, while it is pre-programmed to first sand the leading edge, then clean it, and finally apply a new coating.
The new robot will also have the ability to be remote controlled directly by a trained technician in a control room far away from the actual turbine. That is why the robot is teleoperative. Thus, the robot becomes more versatile and precise, and maintenance work can be tailored to special tasks on each turbine.
- As it is now, we can solve the more uniform maintenance tasks, but with a teleoperative robot, the robot will also be able to handle special and complex types of damage that may occur on wind turbines, explains Martin Huus Bjerge, CEO of Rope Robotics.
Haptic feedback and VR
The actual control of the robot will be done with a so-called master robot. It works a bit like a joystick and consists of a robot arm that can be controlled using the technician's own arm.
Through haptic feedback such as vibrations and temperature fluctuations that can be felt on the skin, the technician will be able to sense the material and the tool and adjust the work in progress. The haptic feedback will be provided by researchers from Aarhus University.
The technician will also wear VR glasses and through cameras on the robot, be able to see the work on the wind turbine in three dimensions. This part will be developed by Xplor XR in cooperation with Innopixel.
They will also be responsible for designing the training platform that will be necessary to teach technicians how to operate the robot.
Many possible applications
Initially, the robot will be developed to perform maintenance on the leading edge of wind turbine blades, the so-called leading edge erosion. In Scandinavia, the blades are worn down by rain that hits them as they spin around at speeds of up to 300-400 kilometers per hour. In other parts of the world, sand can be the problem.
However, the ambition is for the robot to also be able to perform a wide range of other tasks, such as replacing the lightning conductors that are crucial to wind turbines.
- There may also be small cracks in the blades that come from the great stresses the blades are subjected to during operation, says Martin Huus Bjerge.
- There can be all kinds of cracks in the fiberglass that need to be repaired. And since the robot is already up there to maintain the leading edge, it's smart if it can also take care of them.
Meet the researcher
Cheng Fang is an associate professor in SDU Robotics at the Maersk Mc-Kinney Moller Institute.
Facts
- SENSIBLE stands for Symbiotic tEleoperatioN for Safe and cost-efficient wInd turBine bLade maintEnance.
- The goal is to further develop Rope Robotics' existing robot for wind turbine maintenance, so that it can be remotely controlled by a technician from a long distance.
- The project is a Grand Solutions project and has received 12.7 million DKK in funding from the Innovation Fund. The total budget is 17.1 million DKK.
- The partners are the University of Southern Denmark, Aarhus University, Rope Robotics and Xplor XR in collaboration with Innopixel.