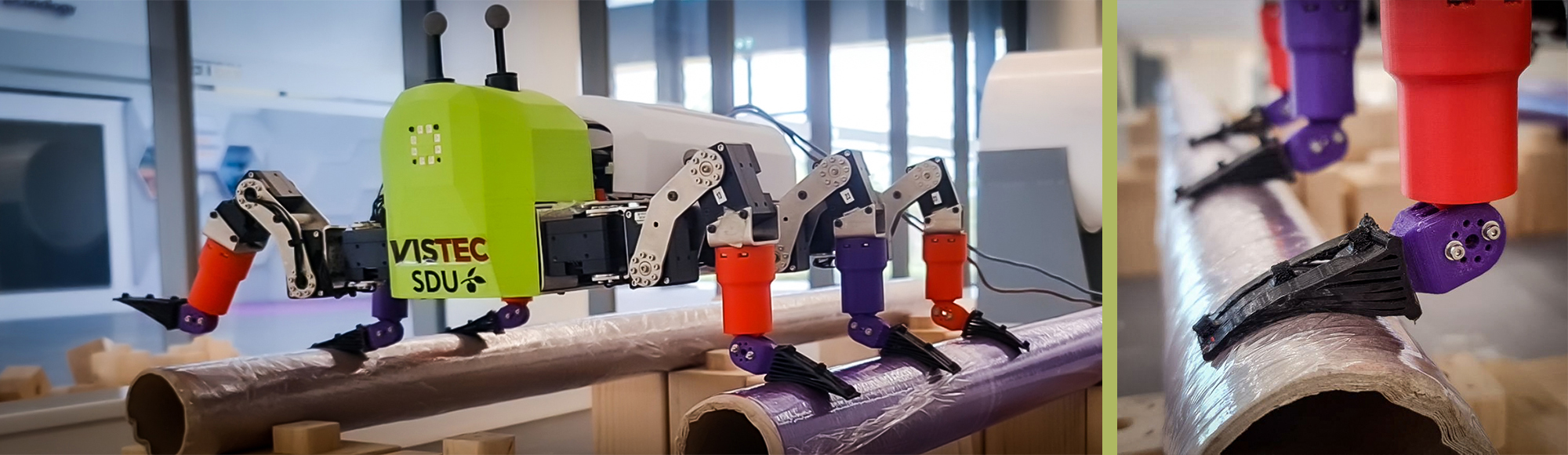
Researchers find inspiration from insects to give robots a better grip
Researchers from universities in five countries are behind insect-inspired robot technology that break with 25-year-old gripping technology - the result is creating international attention.
Just by changing the angle in constructing a robot gripper, a team of researchers from universities in five countries has refined a technology that can change the entire robot industry's way of producing grippers and feet for robots. The inspiration came from insects.
Almost a quarter of a century after German biologist Leif Kniese introduced the interesting bending behavior of the fin of a fish (known as Fin Ray® effect) which has been utilized for a robot gripping mechanism, an international research team, led by Professor Poramate Manoonpong from Syddansk University (SDU) in Odense, now refines the technology that has been used ever since.
The SDU-professor has worked on the project with fellow researchers from Kiel University (Germany), London South Bank University (UK), Islamic Azad University (Iran), and Vidyasirimedhi Institute of Science and Technology (Thailand) to achieve the results, that has recently been published in the recognized journal Advanced Intelligent Systems.
”It means that we can save up to around 20 percent of the energy, but it also that we can take a more gentle approach and, among other things, use the gripping mechanism for a robot gripper to handle very delicate and fragile items like foods
They moved focus from fish to insect to improve the gripping mechanism which can be applied for the feet of a legged robot and the grippers of a robot arm. The refined technique can change the entire robot industry's way of producing grippers for robots.
In the traditional Fin Ray® -based gripping mechanism from Kniese, transverse beams of 90 degrees were used in the triangular shape, which means that by adding force and pressing together the gripping mechanism is made to bend "inward" around the object.
- It has been considered the most optimal form, and this is the first time anyone has looked at other methods. We could see that the angle of insects’ attachment pads is different, said Poramate Manoonpong, who is professor of biorobotics from The Technical Faculty at Syddansk University (SDU) in Odense.
Can change industry choices
By just changing the angle of the transverse beams in the triangular shape from 90 degrees to other degrees (e.g., 10 or 30 degrees) inspired by insects’ attachment pads, you can achieve a more significant effect, as the gripping mechanism bends even more around the object. And at at the same time is using much less force or energy.
- It means that we can save up to around 20 percent of the energy, but it also that we can take a more gentle approach and, among other things we can use the gripping mechanism for a robot gripper to handle very delicate and fragile items, like foods, and apply significantly less force or energy in the meantime. It could have an impact on the way the entire industry makes grippers, said Poramate Manoonpong.
Inspiration from insects
Since 2018, the research team has taken an inspiration from the biological building blocks in the legs and feet of insects such as crickets, previously investigated by the team of Professor Stanislav N. Gorb from Kiel University in Germany. The new gripping technology can be also used for a robot's feet.
Using the insect-inspired feet, a robot can walk safely along, for example, an oil pipe and perform inspections. Work that today must either be performed manually by humans or by switching off the supply and inspecting the pipe inside by sending in a robot.
- If you use traditional robot feet, a robot can only walk very uncertainly and slowly over impassable terrain - it can be on rocky ground or directly on a pipe, which is something the oil and gas industry demands, said Poramate Manoonpong.
Faster and more secure
The researchers have compared the traditional construction from Kniese with a robot foot with a 10 degree angle on the transverse beams. The results show that the robot gets a better grip when the foot bends around the pipe.
- We could also see that the robot has to use much less energy and moves faster because a more significant part of the foot has contact with the pipe, so it has to use less energy to walk the same distance, the SDU-professor said.
When the researchers applied the foot with a 10 degree angle to each leg of a six-legged robot and let it walk on pipes and rocky ground, they were just as excited to see the robot manages without a complex control. This shows that motion intelligence can be achieved through the body rather than the brain.
Walks with flippers
- We tried first with the classic robot foot, which is very simple and has no large contact surface (less mostly about a table leg), And the robot did not come forward, and if it did, it costs a lot of energy, and it could not go straight, Poramate Manoonpong says.
However, using its triangular foot on the rocky surface, the researchers were stunned.
- It's a bit like a swimming foot, and we would typically never wear them as humans if we had to walk on a rocky beach, for example, laughs Poramate Manoonpong.
There was no laughing but instead cheering among the scientists, for the flippers on the six-legged robot did wonders. Precisely because the foot with the new way of angling the beams can "grab" the stone.
- we could see that the robot can walk quickly and easily across a rocky surface. And it also goes straight - which is entirely impossible if you use traditional robot feet, Poramate Manoonpong says.
Meet the researcher
Poramate Manoonpong is a professor at The Mærsk Mc-Kinney Moller Institute and his research interests are among other things service- and inspection robots.